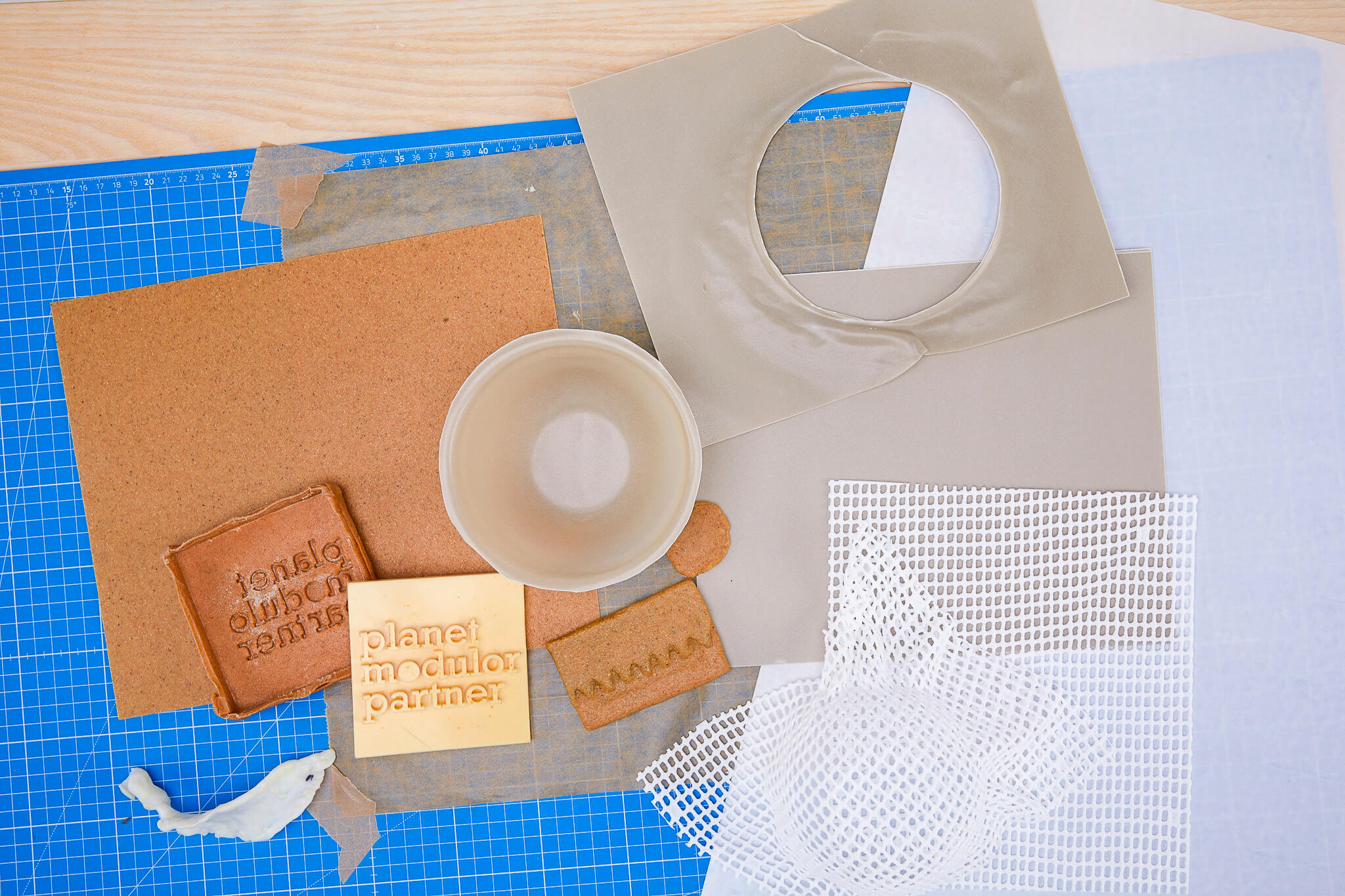
Material des Monats: Worbla & Co.
Schon öfters wurden hier im Magazin die Vorzüge thermoplastischer Kunststoffe dargestellt. Das Formen von Thermoplasten ist im Vergleich zu vielen anderen Werkstoffgruppen recht leicht, da sie durch relativ wenig Wärmezufuhr in einen plastischen – also formbaren – Zustand kommen. Das macht diese Kunststoffe für viele Anwendungen so attraktiv, denn die Kosten (pro Stück) des Formens sind selbst in geringen Stückzahlen häufig überschaubar. Zuerst erwärmen und dann tiefziehen, spritzgießen, extrudieren, biegen, etc. – Warmumformen funktioniert problemlos mit dieser Gruppe von Kunststoffen. Bei Bedarf auch immer wieder.
Naheliegend ist dann sicherlich die Idee, solche Kunststoffe auch für die individuelle Verarbeitung in Bereichen wie Prototyping, DIY, Basteln, Dekorieren oder Reparieren zu nutzen, also für die geringste, denkbare Stückzahl: Eins. Leider werden aber die meisten thermoplastischen Kunststoffe – vom Polystyrol über Acrylglas bis zum Hart-PVC – im Temperaturbereich zwischen 130 °C und 200 °C umgeformt. Bei solchen Temperaturen ist die Bearbeitung dieser Werkstoffe per (ungeschützter) Hand also nicht möglich. Und so blieb diese Werkstoffgruppe handwerkelnden Bastlern lange Zeit weitestgehend verschlossen.
Thermoplastische Modelliermassen, Worbla – was ist das?
Das änderte sich erst mit der Entwicklung von Polyestern, die bei deutlich unter 100 °C bereits formbar sind. Worbla ist beispielsweise aus einem Polyester. Andere modellierbare Kunststoffe werden aus biobasierten Kunststoffen erzeugt und wieder andere aus Polyurethan. Gemeinsam haben sie alle, dass sie bei üblichen Umgebungstemperaturen fest und stabil sind, aber bereits bei Temperaturen, die leicht in jedem Haushalt erzeugt werden können, weich und formbar werden. Wir fassen sie in der Gruppe „Thermoplastische Modelliermassen“ zusammen, wenngleich sie im erkalteten Zustand (zum Beispiel beim Verkauf) keine plastischen Massen, sondern feste Körper sind. Zumeist sind sie in Plattenform im Handel erhältlich.
Sicherlich ist Worbla der prominenteste Vertreter dieser Gattung. Neben Worbla gibt es aber weitere Produkte, die sich mit ihren jeweiligen Qualitäten für bestimmte Anwendungen besonders eignen. Im Weiteren wollen wir diese Qualitäten herausarbeiten, damit Du für Deine Gestaltungsaufgabe jeweils das optimale Material findest.
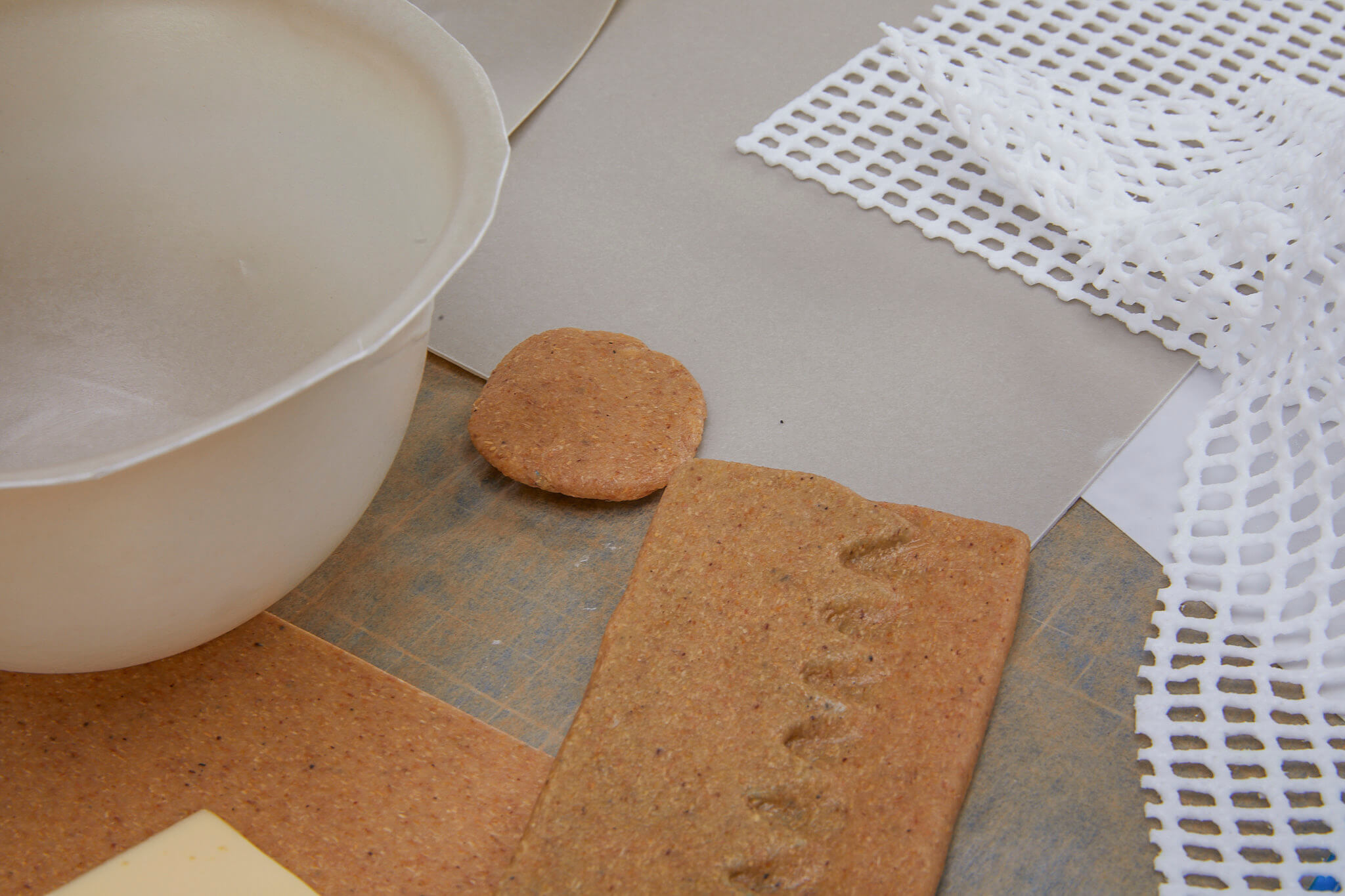
Worbla erinnert immer etwas an Plätzchenteig …
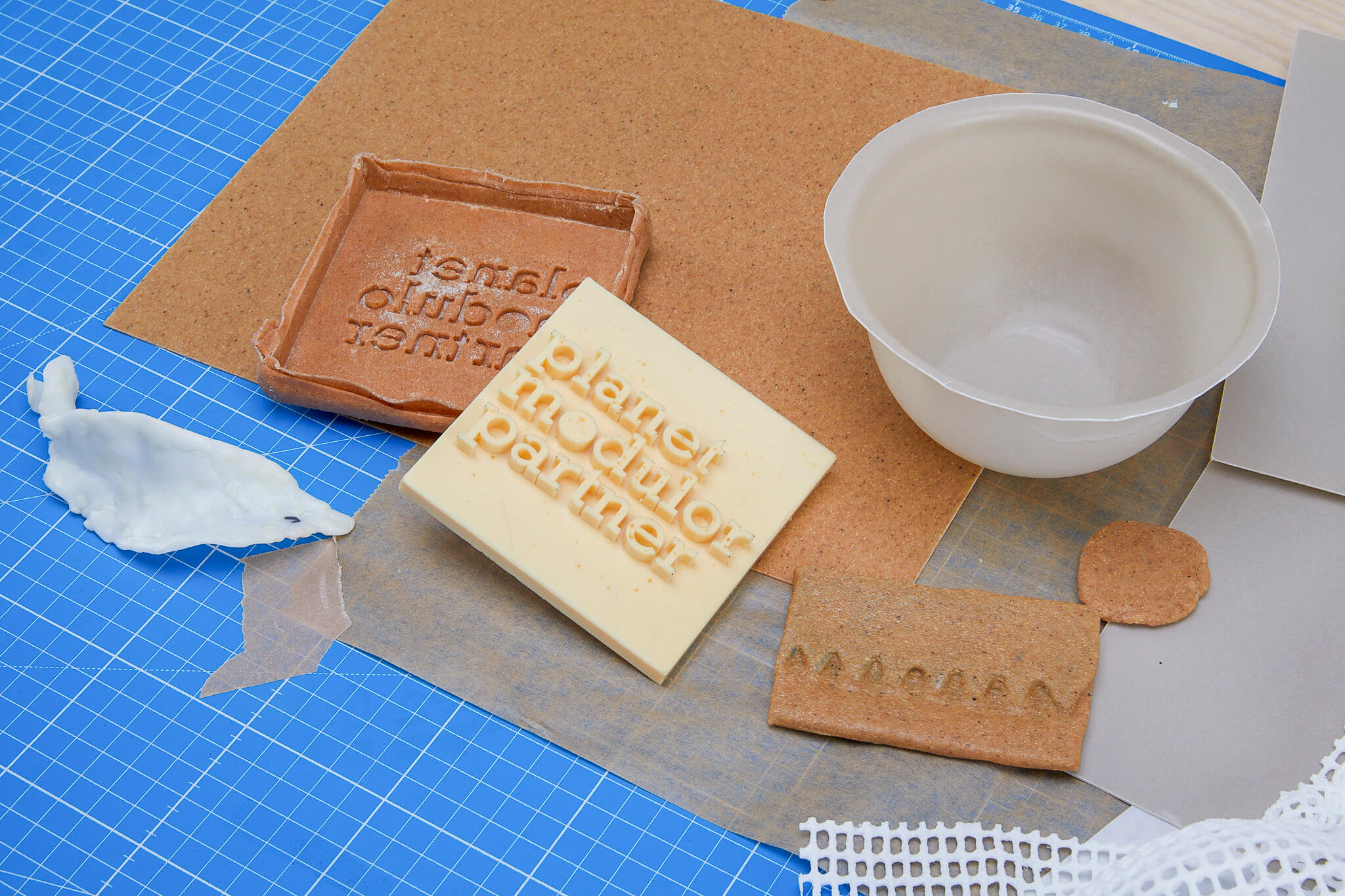
… das braune Material ist Worbla, das hellgraue Thibra und das weiße Gitter ist Varaform
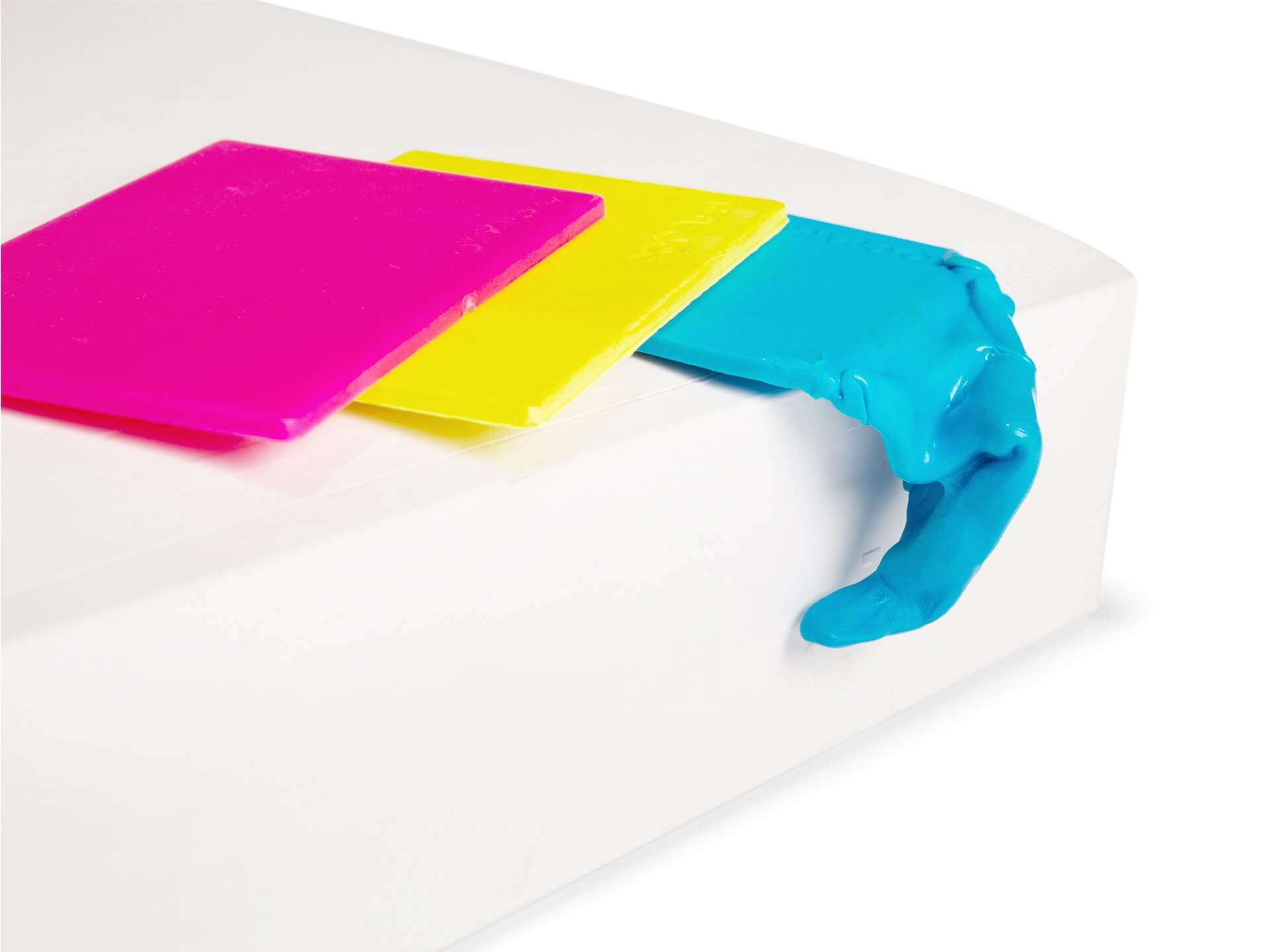
Und außerdem zeigen wir hier noch Formcard
Worbla’s Finest Art – für Cosplay
Worbla’s Finest Art ist für Cosplayer das Material der Wahl. Es besteht aus Polyester und aus verstärkender Zellulose.
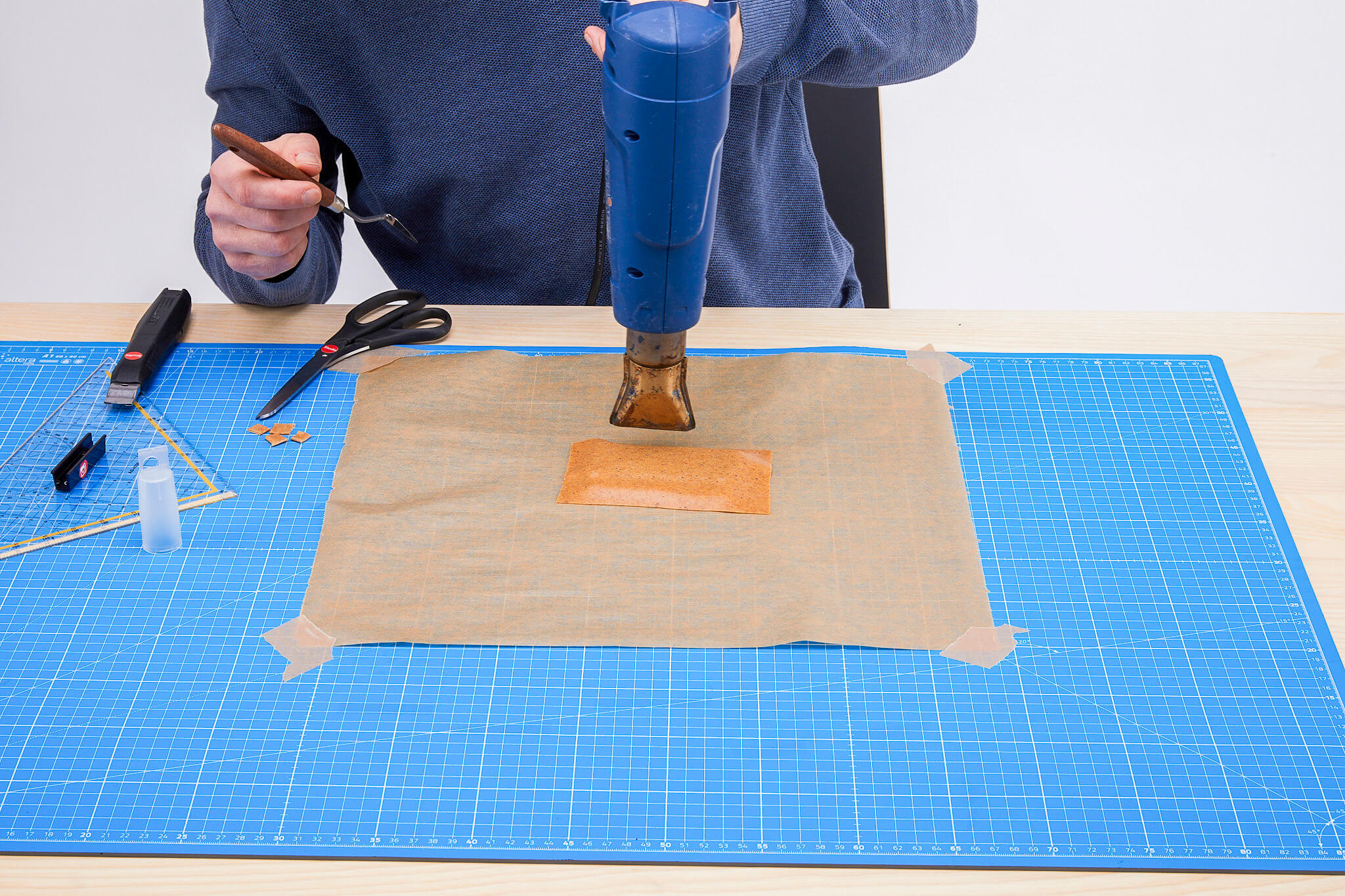
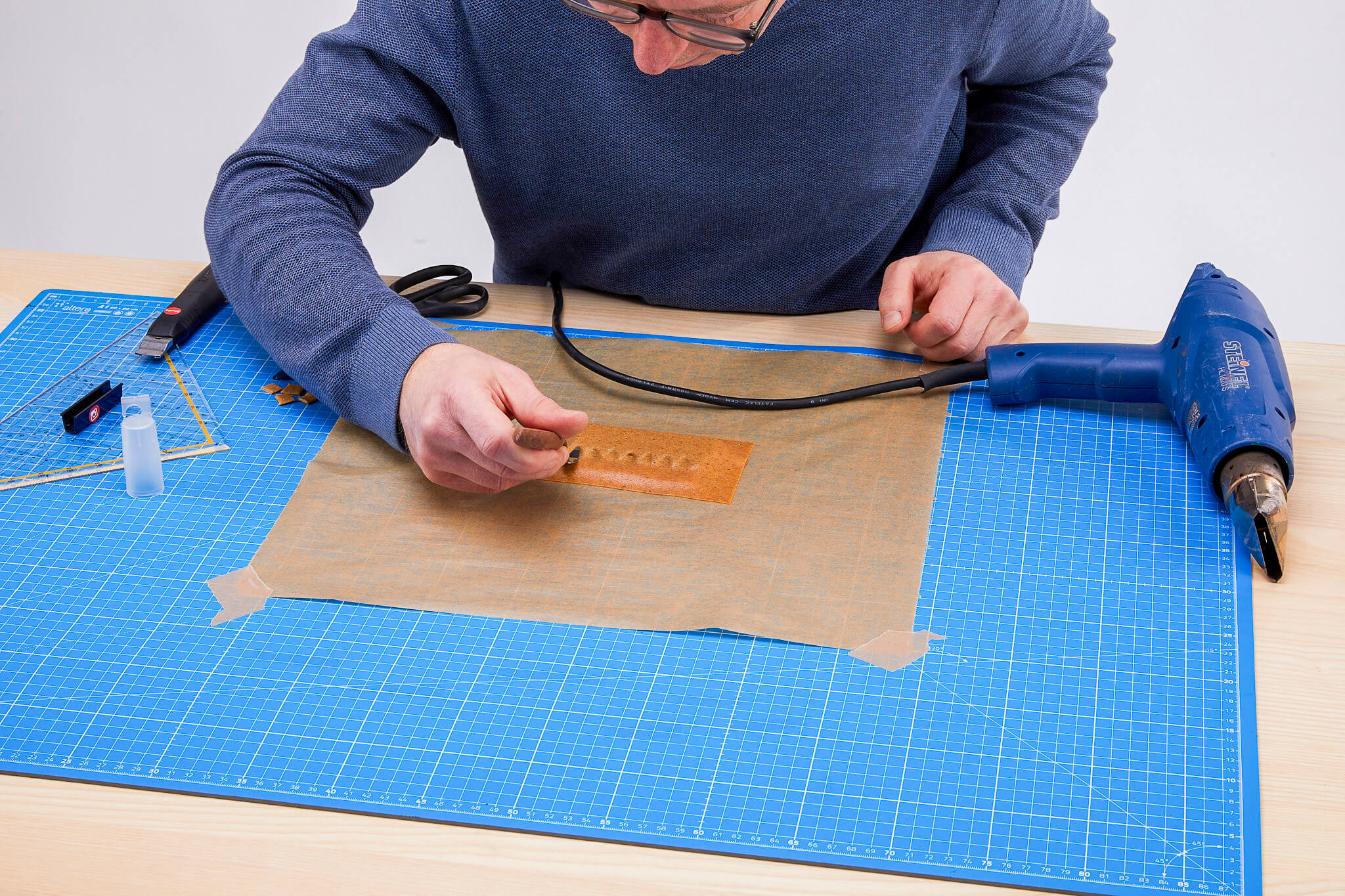
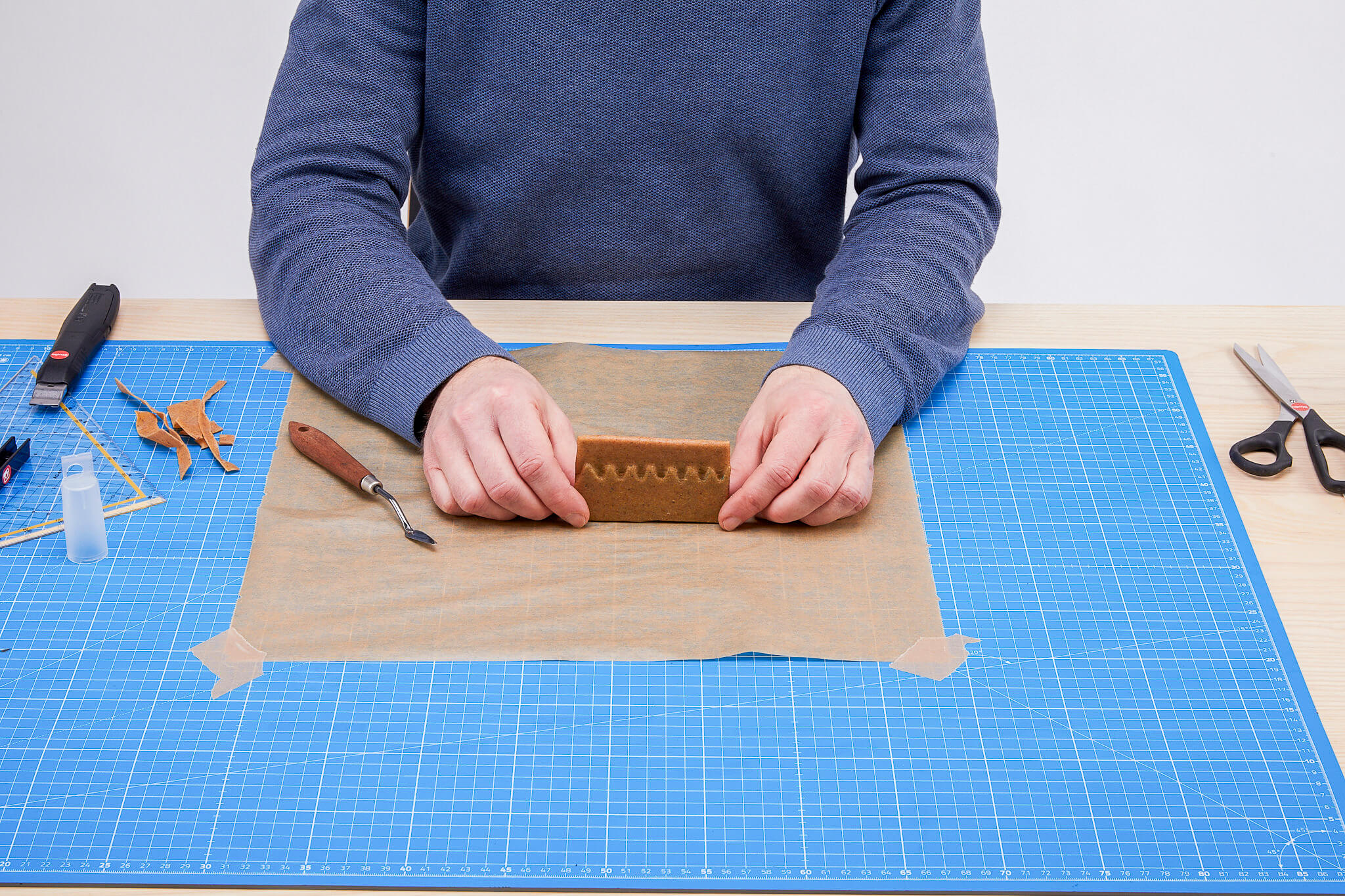
Durch seine Materialeigenschaften eignet es sich für die individuelle Kostümherstellung (z. B. Rüstungen) optimal. Aber auch Figuren und Details lassen sich gut daraus modellieren. Bei Raumtemperatur ist es ein fester plattenförmiger Werkstoff und wird bei 90 °C plastisch formbar und klebend. Im Cosplay sprechen viele vom „Aktivieren“ des Materials bei dieser Temperatur. Durch die zwei Zustände, in denen Du Worbla verarbeiten kannst, ist es auch so vielseitig. Im plastischen Zustand kannst Du es dreidimensional wie Plastilin (Knete) formen und fügen. Wenn es dann wieder abgekühlt und erstarrt ist, lässt es sich sägen, bohren und schleifen. Zu guter Letzt wird es dann grundiert und farbig gestaltet.
Gut zu wissen: Ganz gleich, in welchem Zustand Du Worbla bearbeitest, es ist immer ungiftig und damit gesundheitlich unbedenklich. Und das Gute an Worbla ist auch, dass Reste im erwärmten Zustand zusammengeknetet, gegebenenfalls ausgerollt und später wieder verarbeitet werden können. Du brauchst also nichts wegzuwerfen.
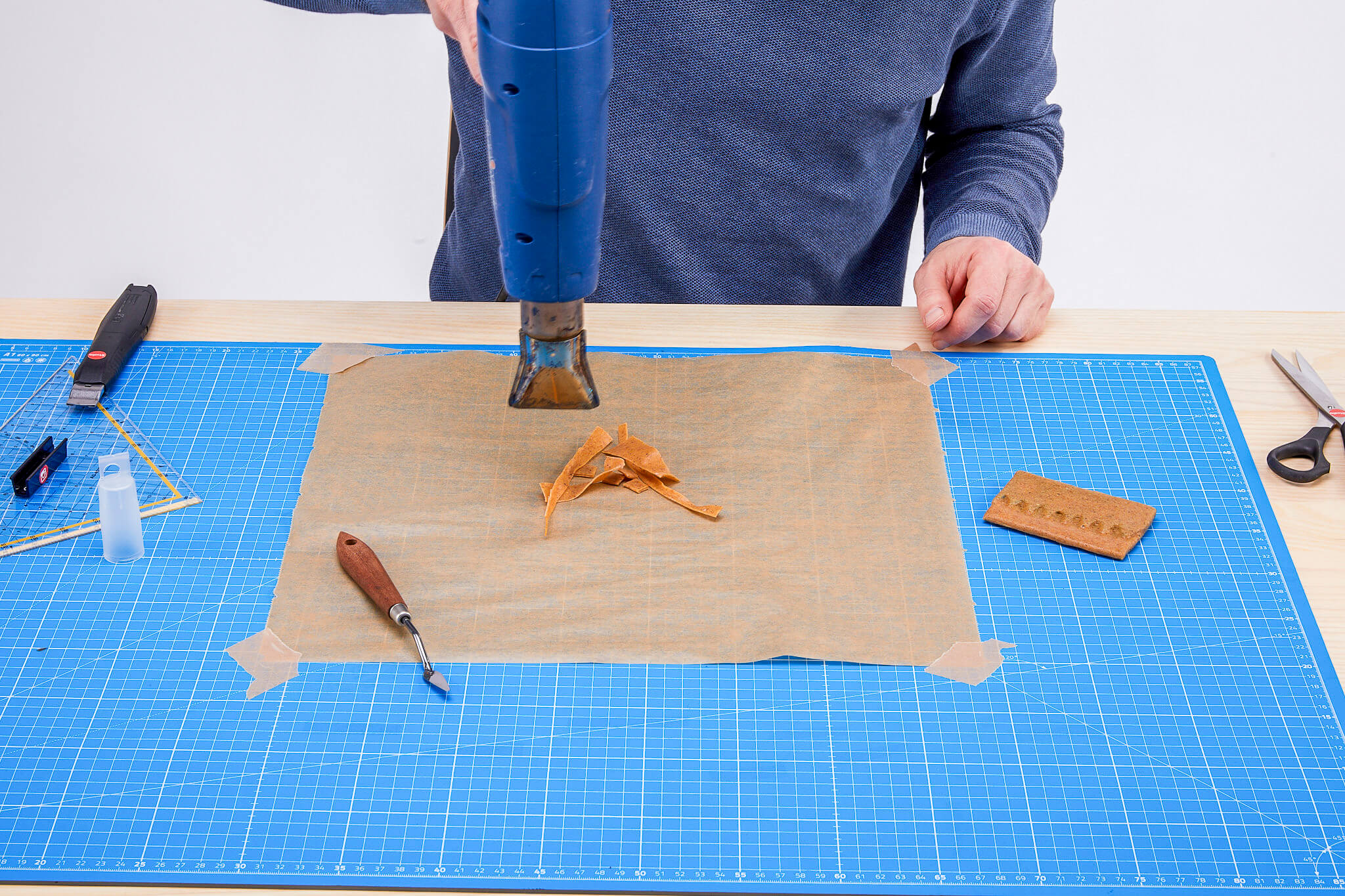
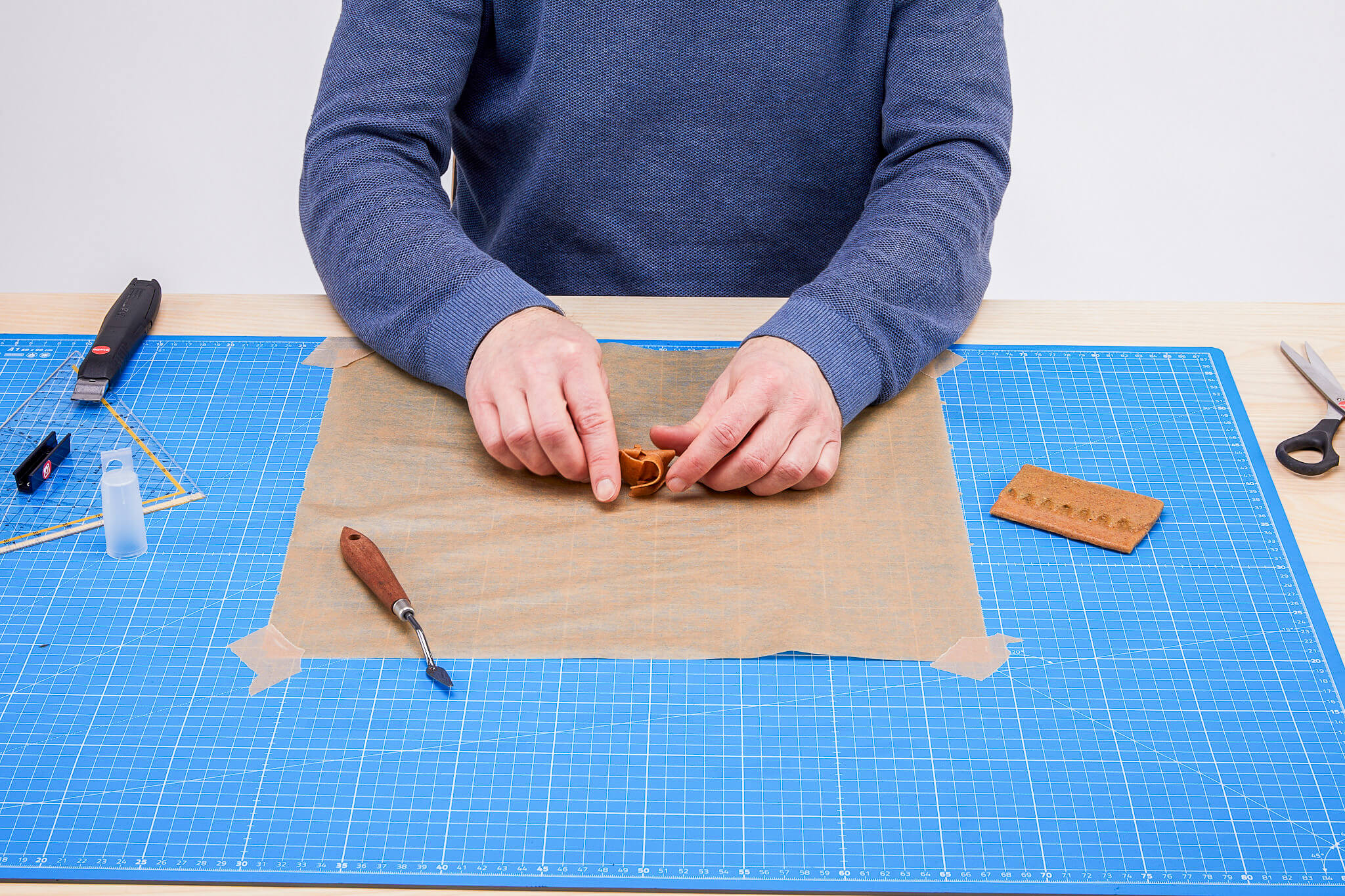
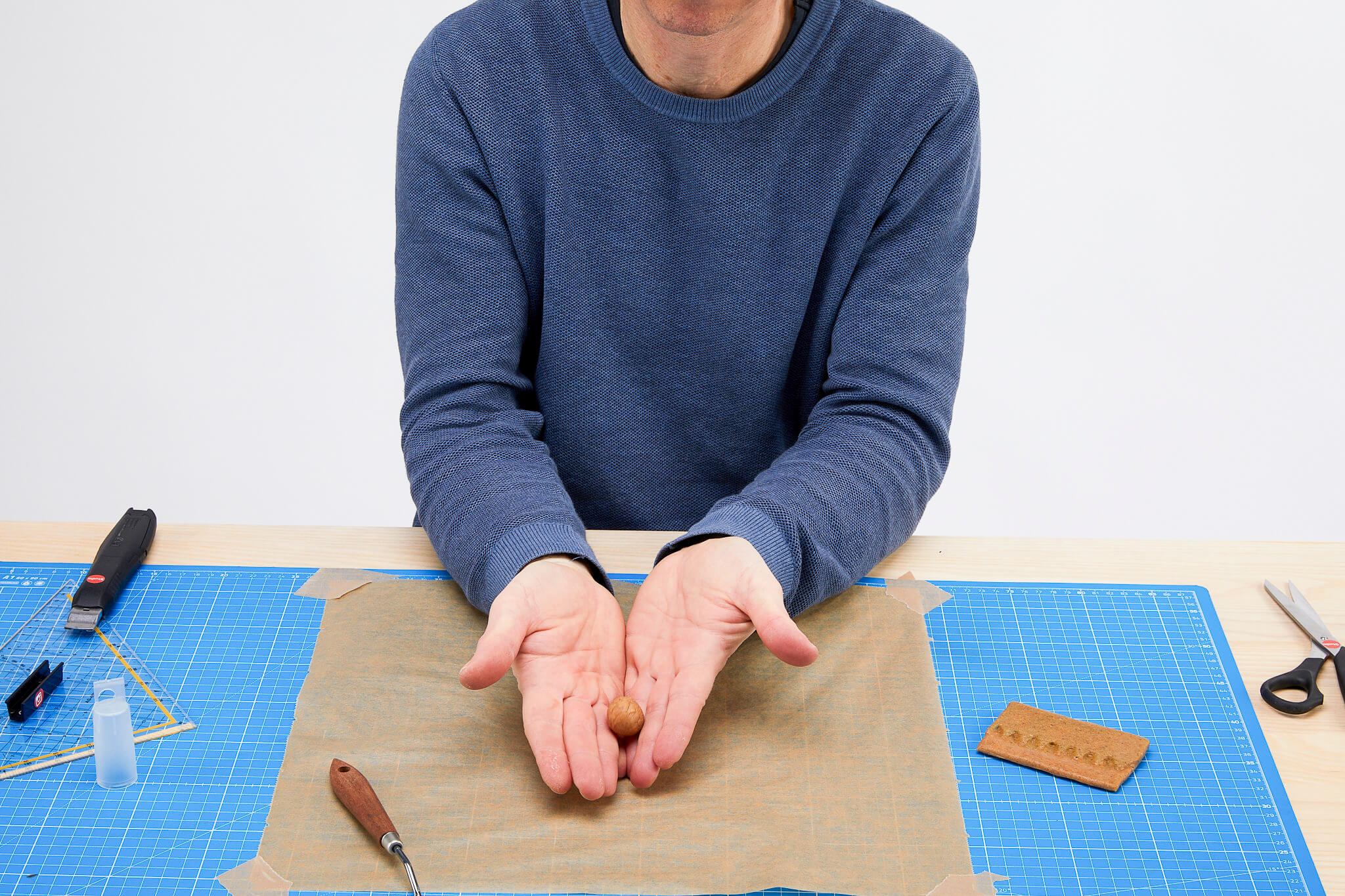
Die Worbla-Platten haben zwei unterschiedliche Seiten. Die eine Seite ist recht rau. Sie wird häufig als sichtbare Seite verwendet. Je nach gewünschter Glattheit wird sie vor dem farbigen Gestalten in mehreren Schichten grundiert. Dafür kannst Du Holzleim oder das auch in der Malerei als Grundierung dienende Gesso verwenden. Die andere Seite ist glatt und glänzt sogar. Auf dieser Seite ist ein Klebstoff aufgetragen, der auch durch Wärme aktiviert wird. Im abgekühlten Zustand ist also auch diese Seite nicht klebend.
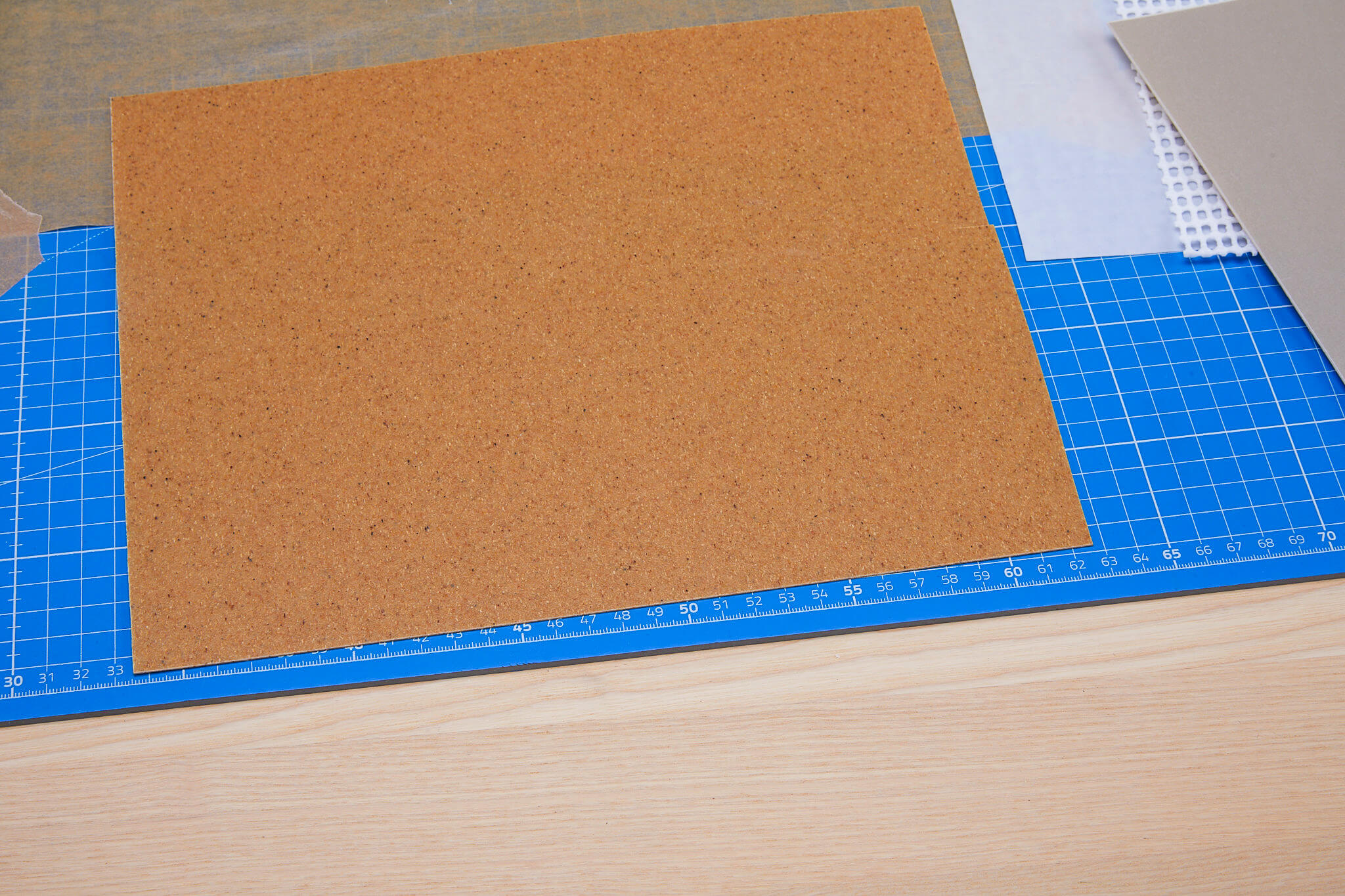
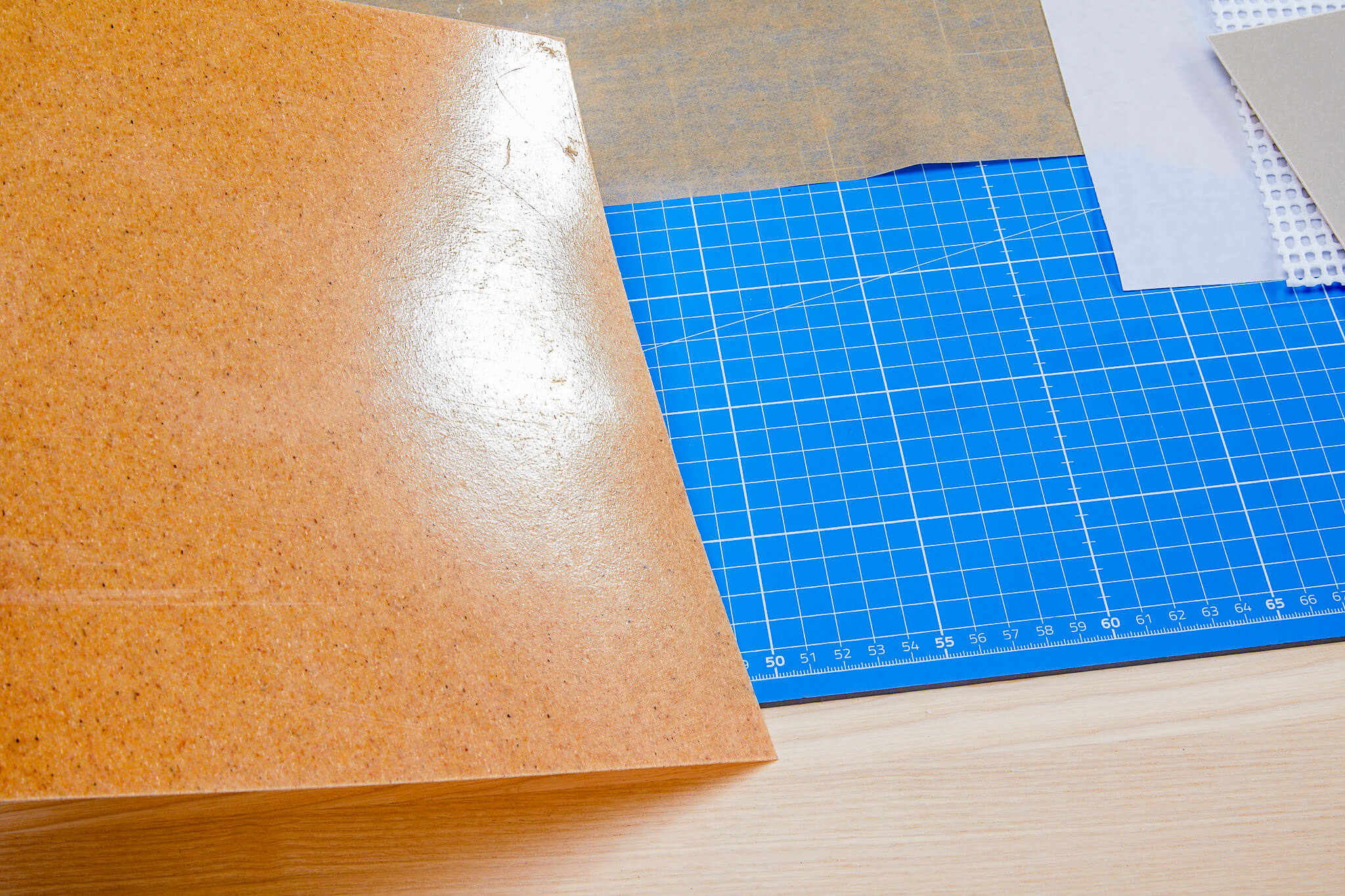
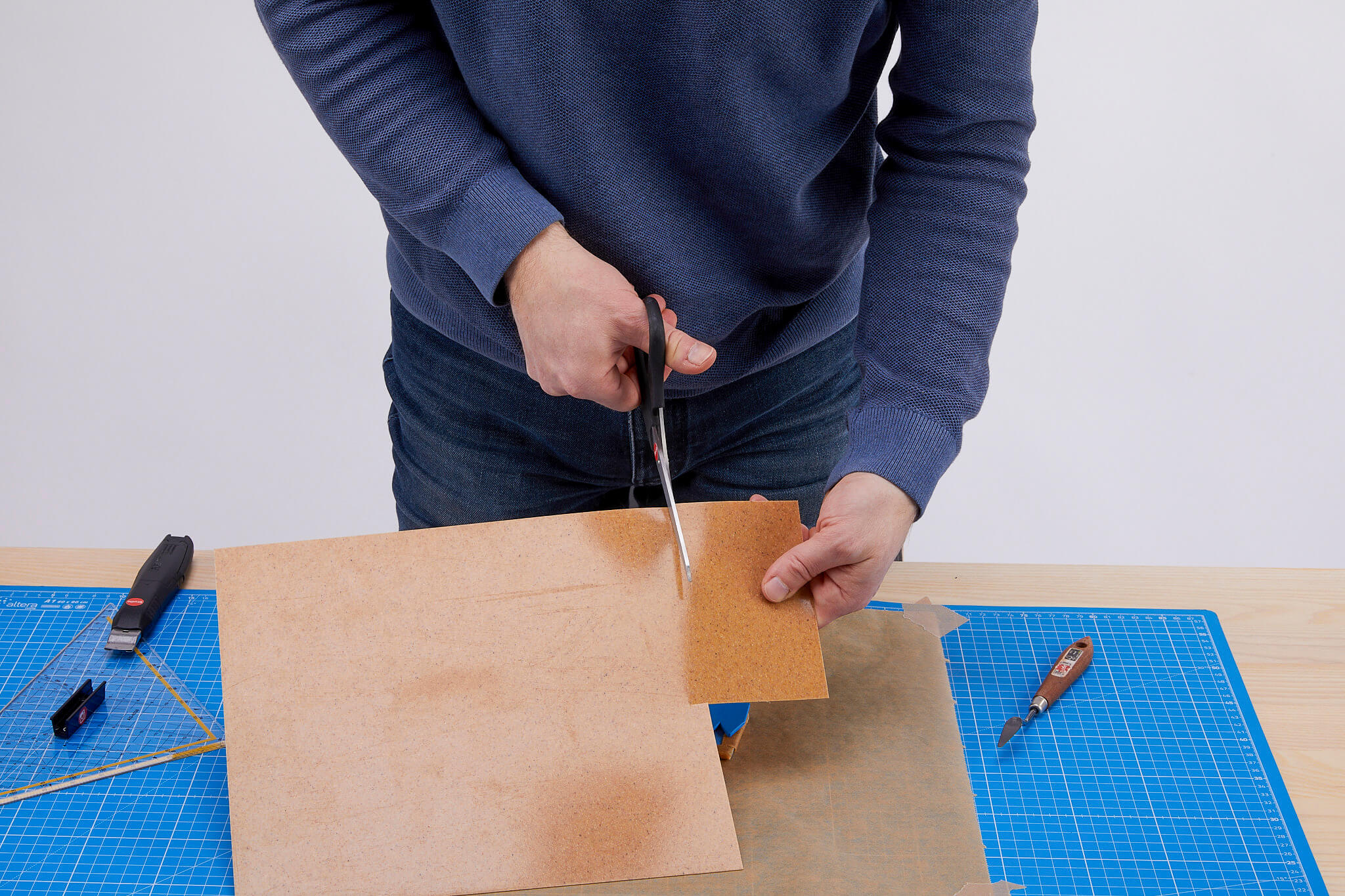
Soll eine Rüstung oder ein Armschutz oder Ähnliches für Showkämpfe stabiler werden und damit auch etwas stärkeren Schutz bieten, kannst Du eine mehrlagige Sandwich-Konstruktion mit Moosgummi im Kern herstellen. Dabei wird auf das zugeschnittene Moosgummi beidseitig Worbla im erwärmten Zustand aufgeklebt, so dass Du ein dreilagiges Material herstellst, das Du weiter dreidimensional formen kannst. Farbig gestaltet wird (bei Bedarf nach dem Grundieren) am Ende häufig mit Acrylfarben. Nach dem Bemalen ist Worbla zwar immer noch mit Hilfe von Wärme wieder formbar. Bedenke aber, dass Du dann zumeist die farbige Gestaltung zerstörst.
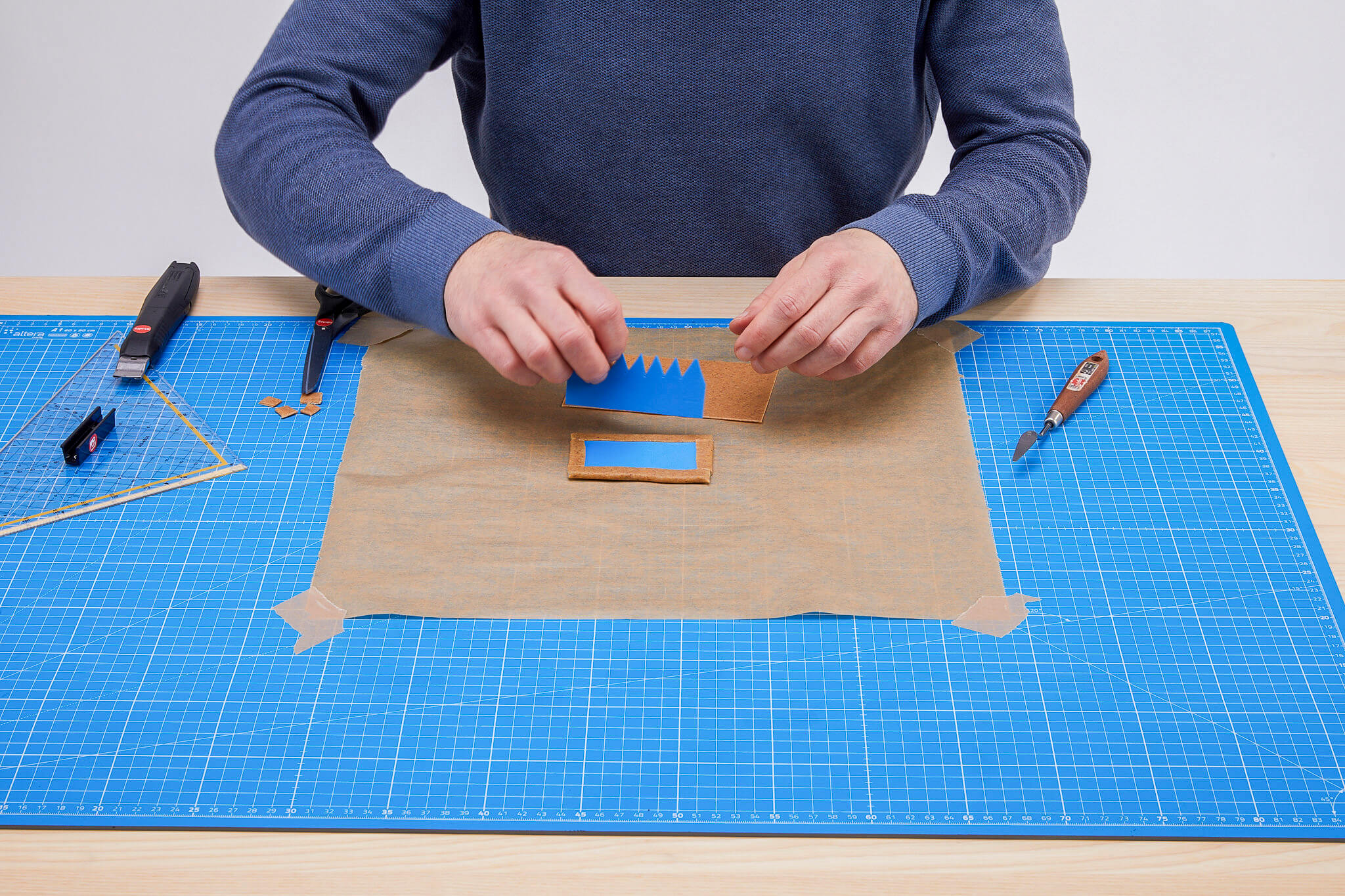
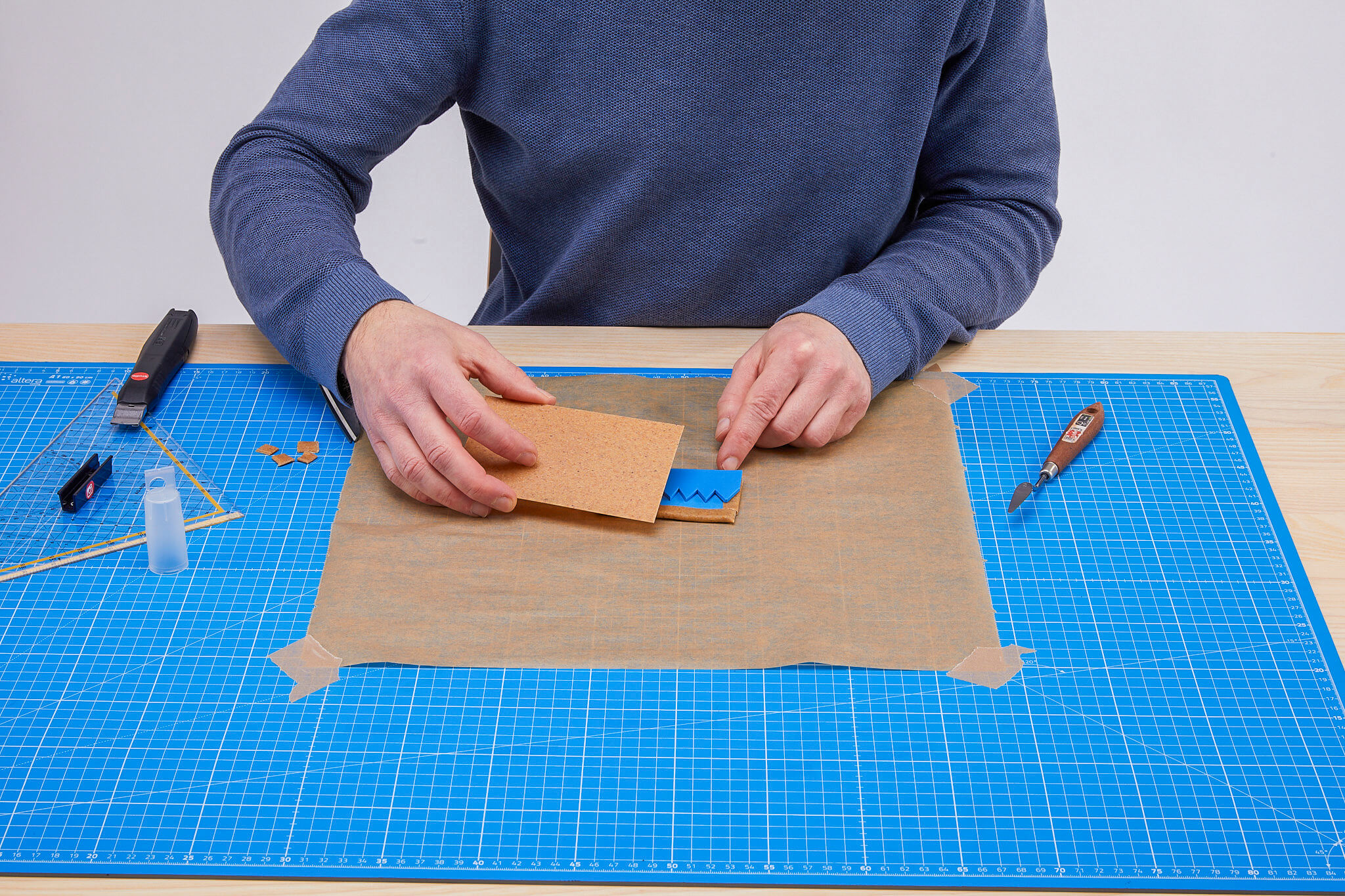
Worbla’s Transpa Art – klar!
Die transparente Variante von Worbla hat etwas andere Eigenschaften als die undurchsichtige, braun-orangene Worbla’s Finest Art. Einerseits gibt es die klebende Seite nicht, andererseits musst Du das transparente Worbla höher erwärmen, um es in den formbaren Bereich zu bringen.
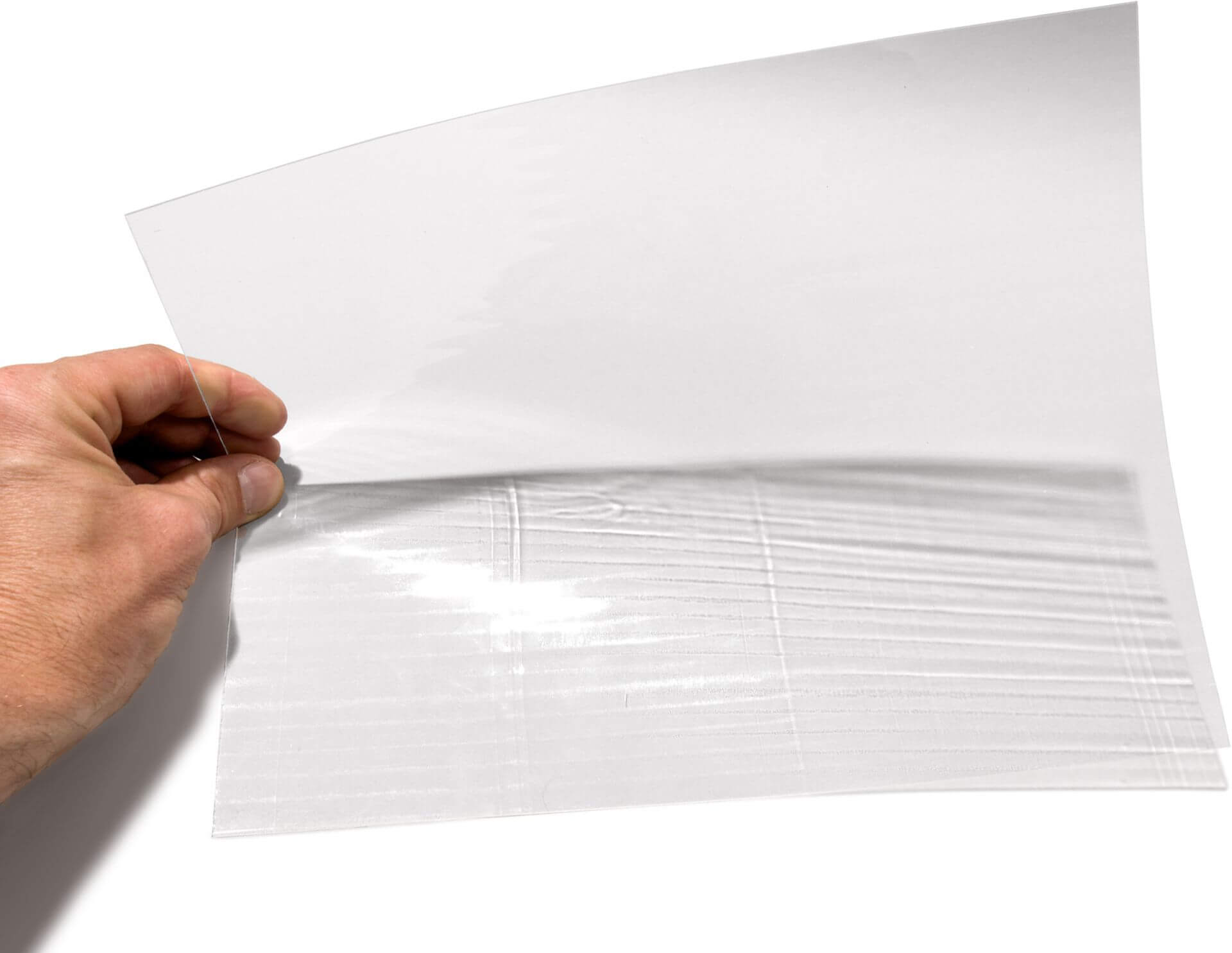
Diesen erreichst Du bei 120 °C – also trage besser Handschuhe. Aber aufgepasst: Ab 140 °C schlägt das Material bereits Blasen, die Du auch nach dem Abkühlen noch sehen wirst. Du solltest also gut aufpassen, das Material nicht zu stark zu erwärmen. Insofern ist es etwas unkomfortabler in der Verarbeitung, aber dafür ist es eben schön durchsichtig. Reste des transparenten Materials lassen sich zwar auch zusammenkneten, darunter leidet aber ein wenig die Durchsichtigkeit. Je häufiger Du das Material verknetest, umso trüber wird es. Willst Du das transparente Worbla verkleben, nutze am besten Sekundenkleber.
Thibra – tiefziehen schon bei 70 °C
Ähnlich wie Worbla ist auch Thibra ein plattenförmiger Werkstoff, der bei Raumtemperatur hart und fest ist und den Du durch Erwärmen in den formbaren Zustand bringen kannst. Thibra ist beidseitig glatt (deutlich glatter als Worbla) und hat eine matte Oberfläche. Es lässt sich sehr geschmeidig formen, ist bereits bei 70 °C im plastischen Bereich und legt sich ausgezeichnet faltenfrei um dreidimensionale Formen. Du kannst es also quasi zum Tiefziehen von Hand verwenden, denn es streckt sich recht weit, ohne zu reißen. Daneben kannst du das Material immer wieder erwärmen und die Form korrigieren. Und aufgrund des niedrigen Temperaturbereichs, in dem Thibra formbar wird, lässt es sich auch mittels ganz verschiedener Wärmequellen auf die nötige Temperatur bringen: Per Heißluftfön, im Backofen und sogar im Wasserbad ist das Erwärmen möglich.


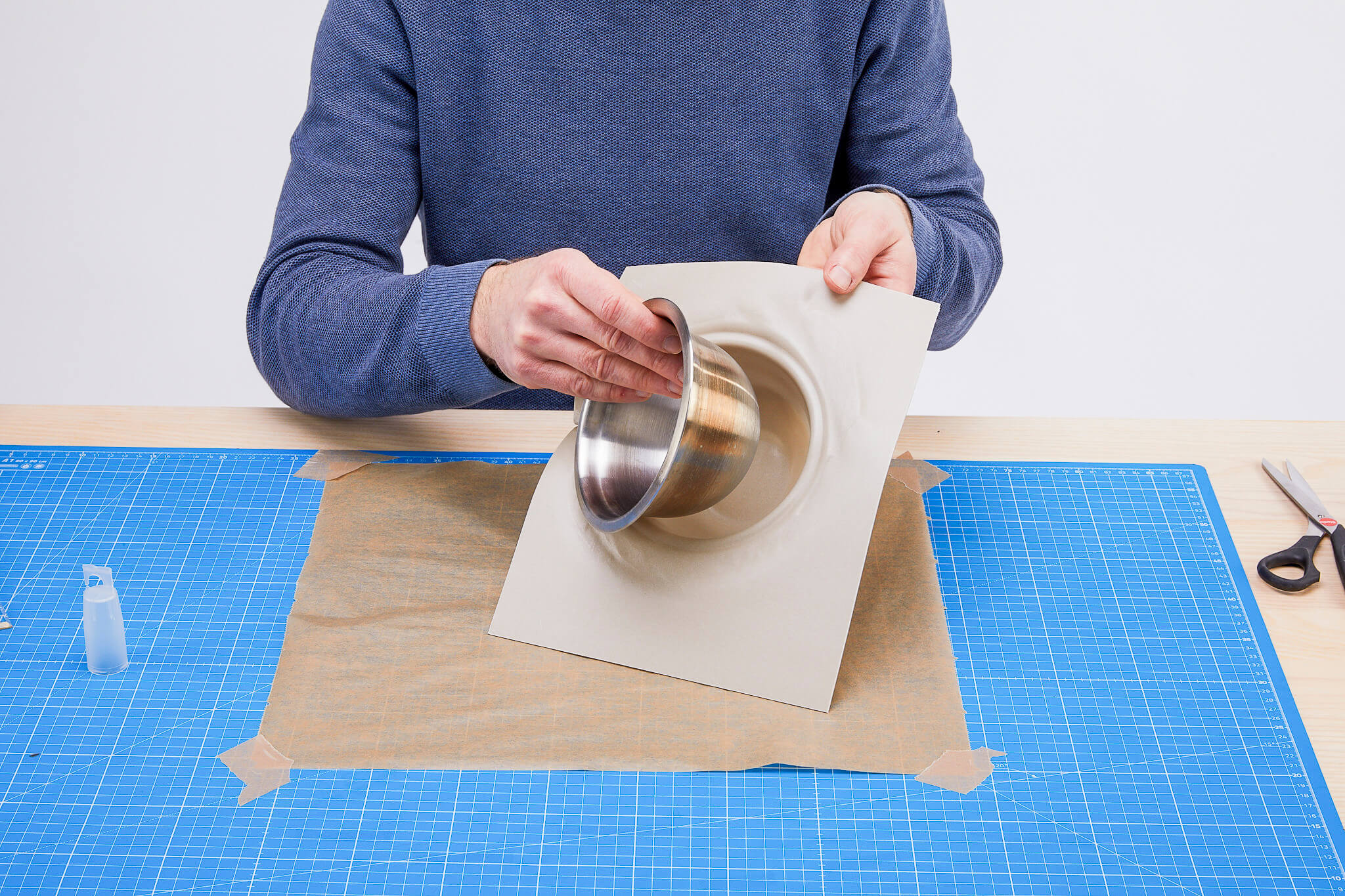
Thibra Pearl – Perlen vor der Form
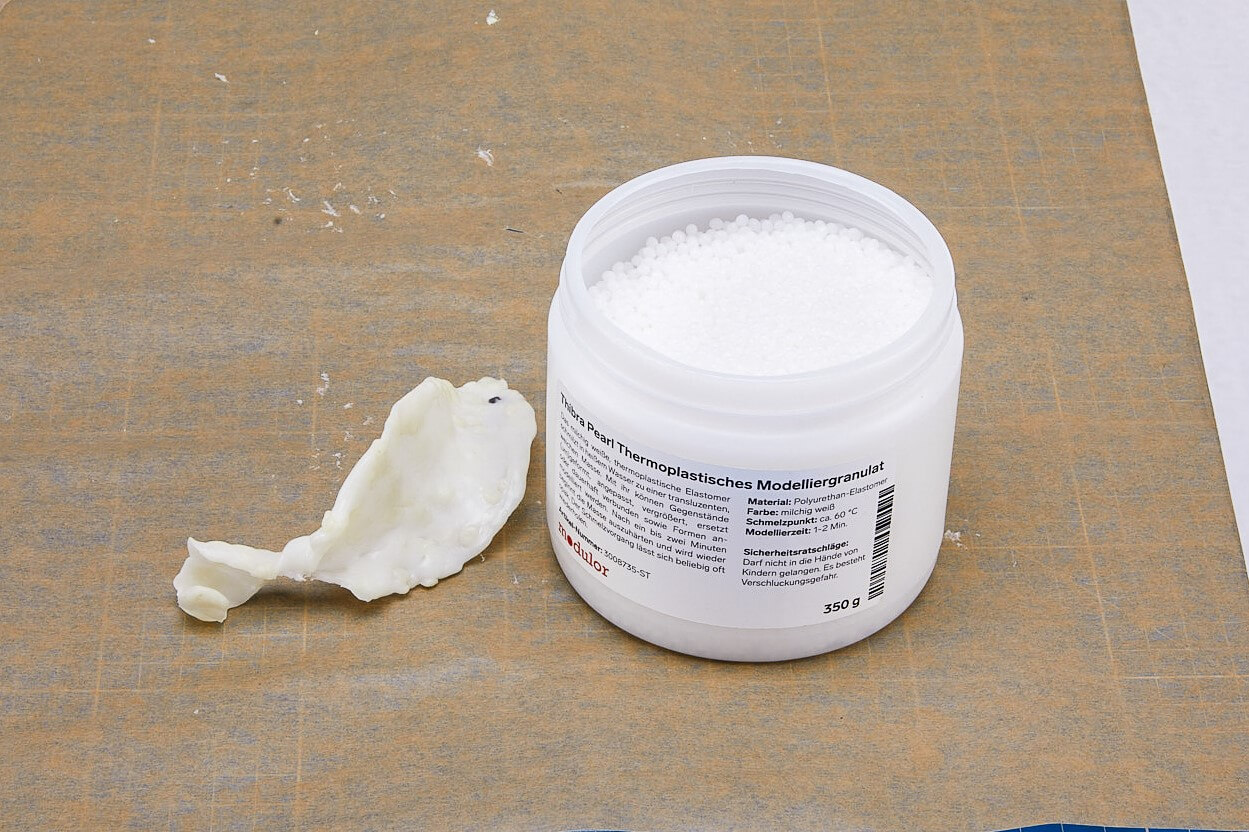
In unserem Sortiment ist Thibra Pearl der formbare Thermoplast, der die niedrigste Umformtemperatur braucht. Bereits bei 60 °C geht das Formen des Polyurethan-Elastomers los. Gut zu kontrollieren ist die Temperatur beispielsweise im Wasserbad, das zum Aufheizen des Materials genutzt werden kann. Die Perlen (bzw. das Granulat) werden oberhalb von 60 °C zusammengeknetet, wobei eine homogene Modelliermasse entsteht, die Du von Hand, aber auch mit Hilfe von Modellierwerkzeugen, in die gewünschte Form bringen kannst. Und wenn das Material abkühlen sollte, bevor Du fertig bist mit dem Formen, erwärmst Du es einfach erneut – so oft Du willst.
Auch für Thibra gilt die absolute Unbedenklichkeit hinsichtlich gesundheitlicher Auswirkungen: Der direkte Kontakt zum (erwärmten) Material ist gefahrlos möglich. Das Formen von Hand ist also uneingeschränkt erlaubt. Lediglich die Gefahr von Verbrennungen bei zu stark erwärmtem Material ist natürlich vorhanden.
Formcard – Reparatur-Kitt im Scheckkartenformat
Der Kunststoff, aus dem Formcard besteht, wird etwas unscharf „Biokunststoff“ genannt. Leider ist tatsächlich nicht so leicht zu ergründen, was das chemisch in diesem Fall bedeutet. Der Begriff Biokunststoff deutet nicht zwingend auf biobasierte Rohstoffe, sondern könnte sich auch auf die biologische Abbaubarkeit (zum Beispiel die Kompostierbarkeit) des Materials beziehen. Und in der organischen Chemie ist beides möglich: Biologisch basiert und nicht biologisch abbaubar gibt es genauso wie erdölbasiert und biologisch abbaubar. Wie auch immer: Die Formcard ist als Reparatur-Material gedacht und immer wieder verwendbar. Sie muss also gar nicht entsorgt werden. Das kleine Format passt in jede Brieftasche, ist also leicht überall dabei und mit verbreiteten Mitteln (heißes Wasser + Tasse) kannst Du das feste Material so formbar machen, dass Du von Hand kleinere Reparaturen vornehmen kannst. Das kann der schadhafte Schraubendrehergriff sein, das gebrochene Plastikspielzeug oder der improvisierte Klingenschutz für ein Messer. Formcard ist also weniger zum Gestalten (benutze dafür besser Worbla) als zum Reparieren und Improvisieren.
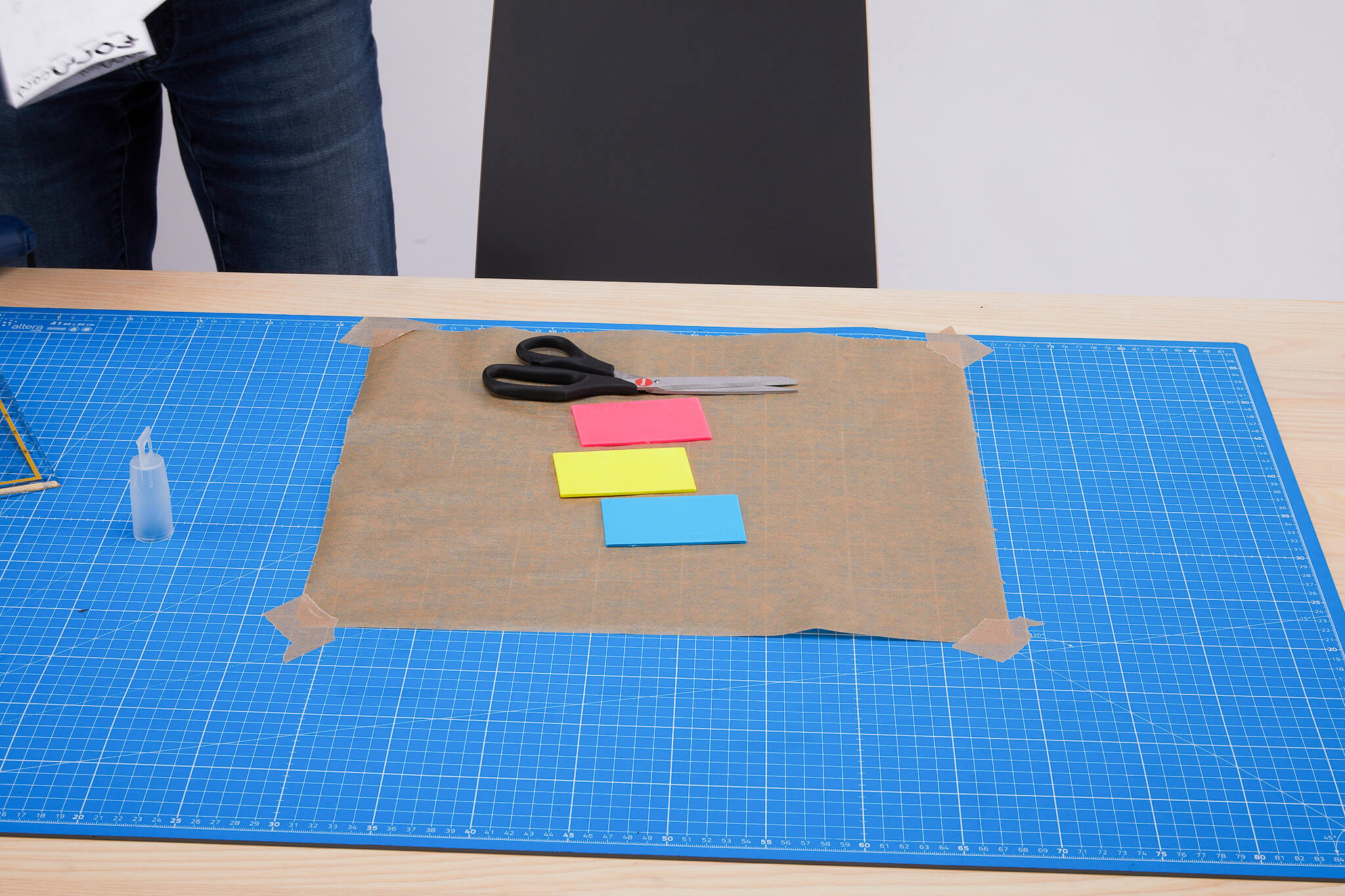
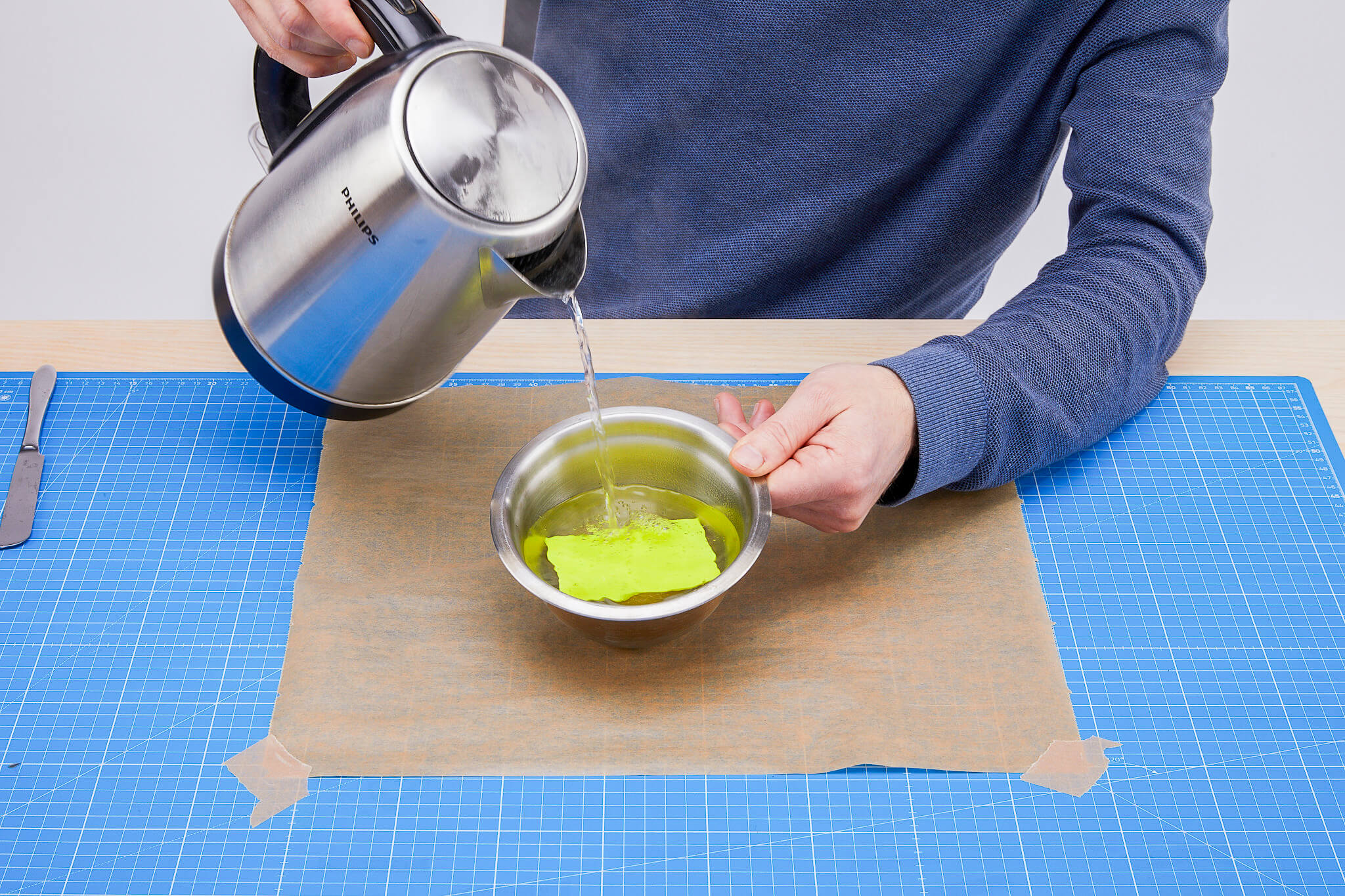
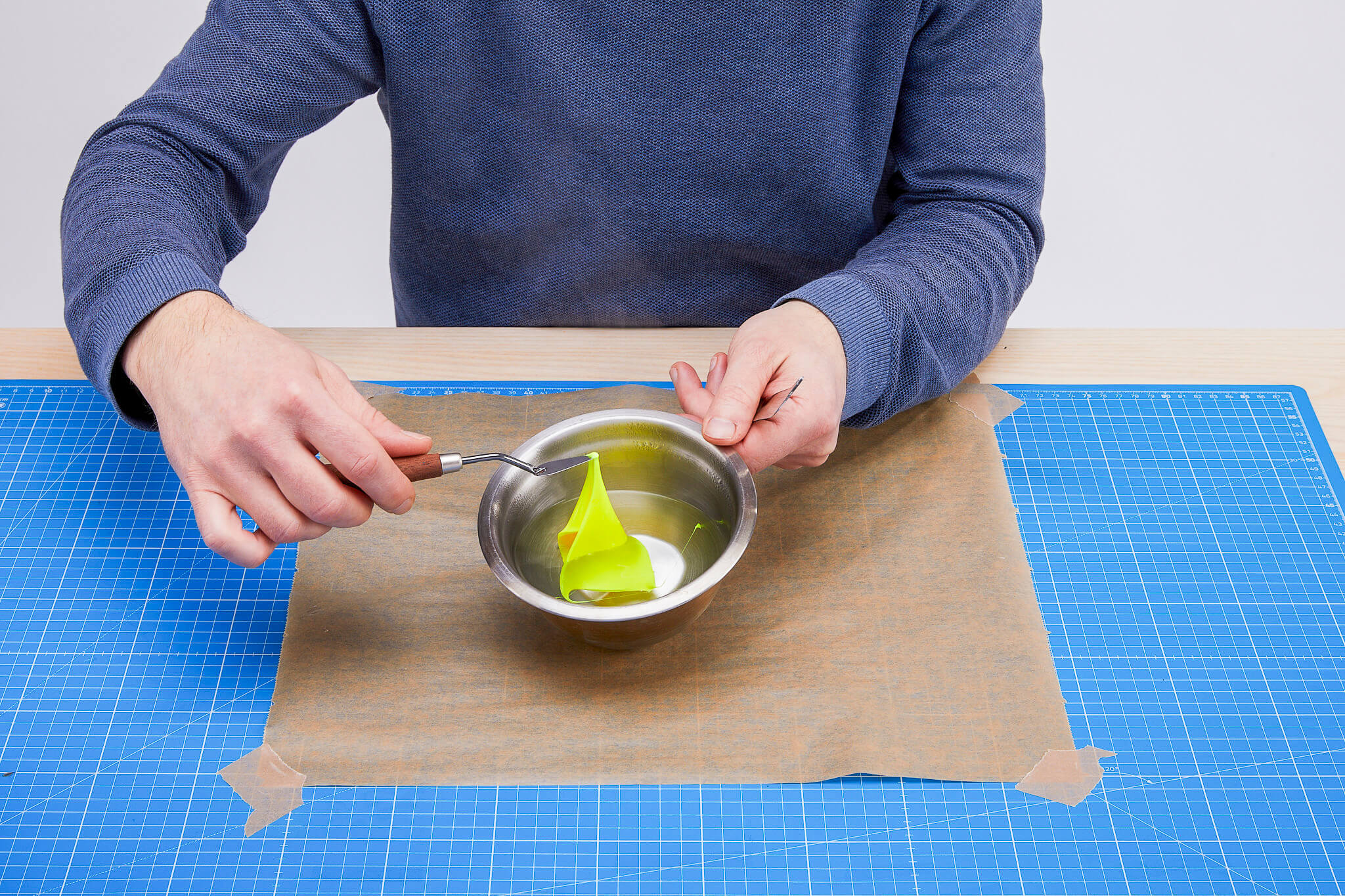
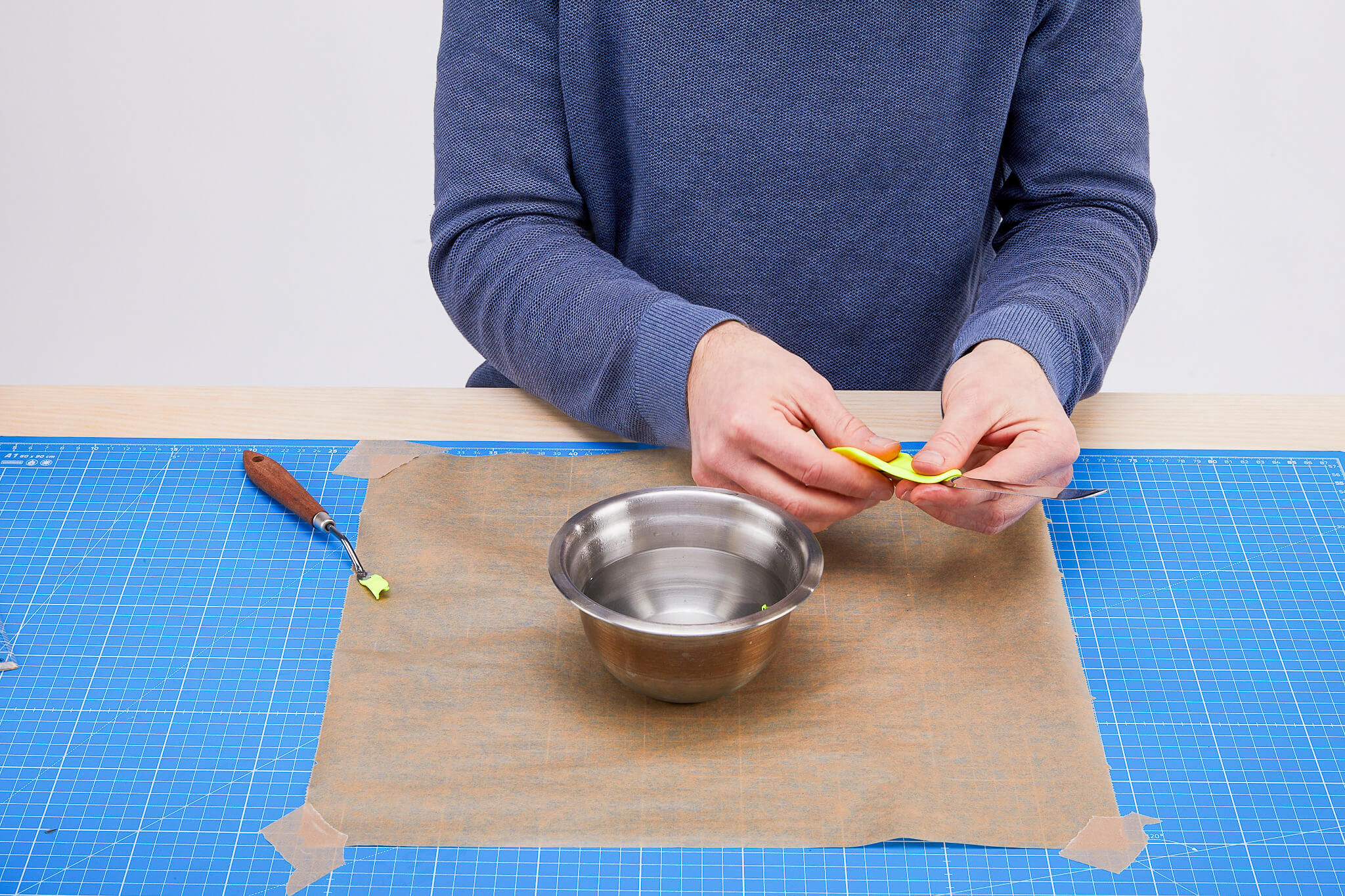
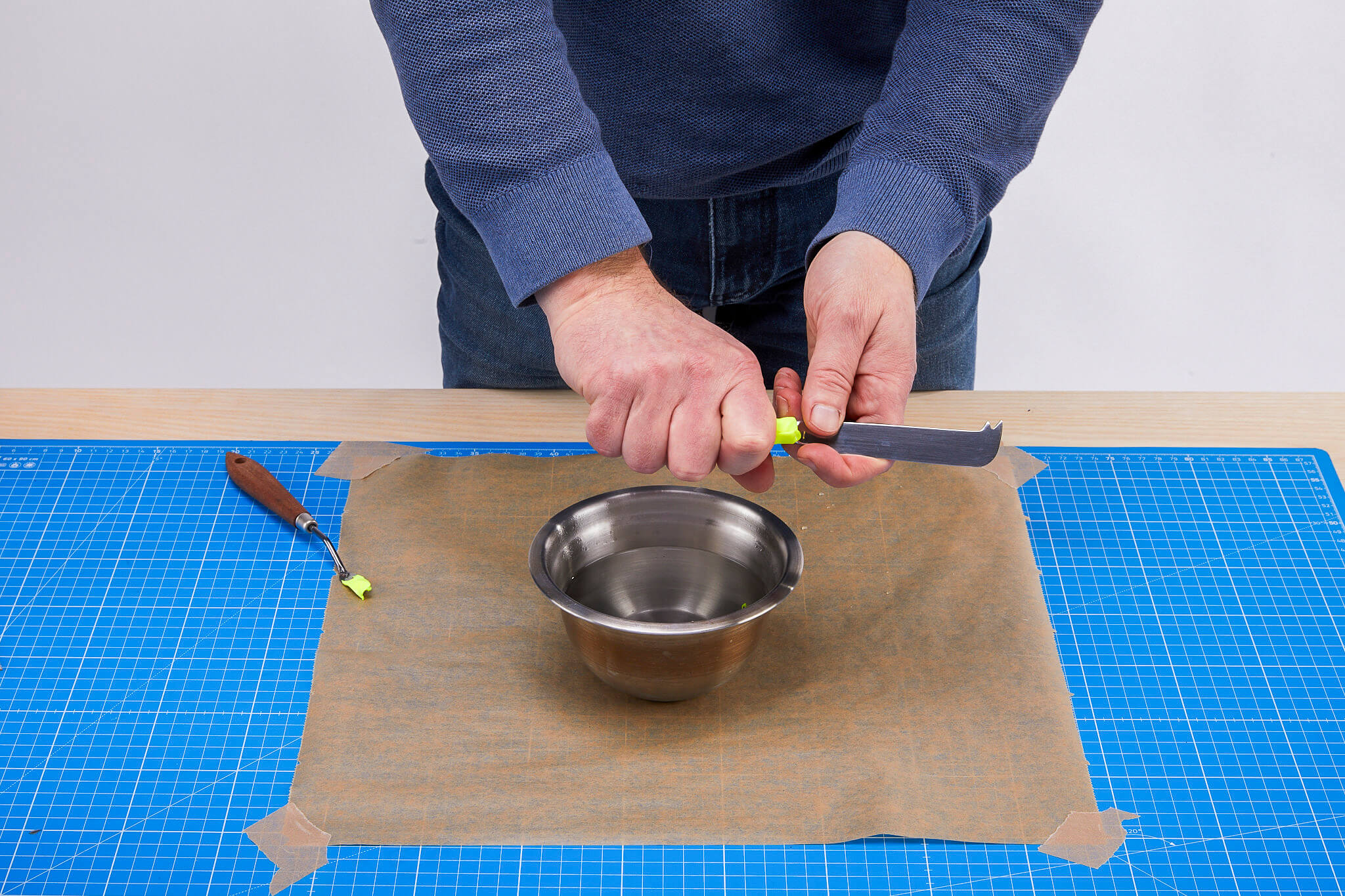
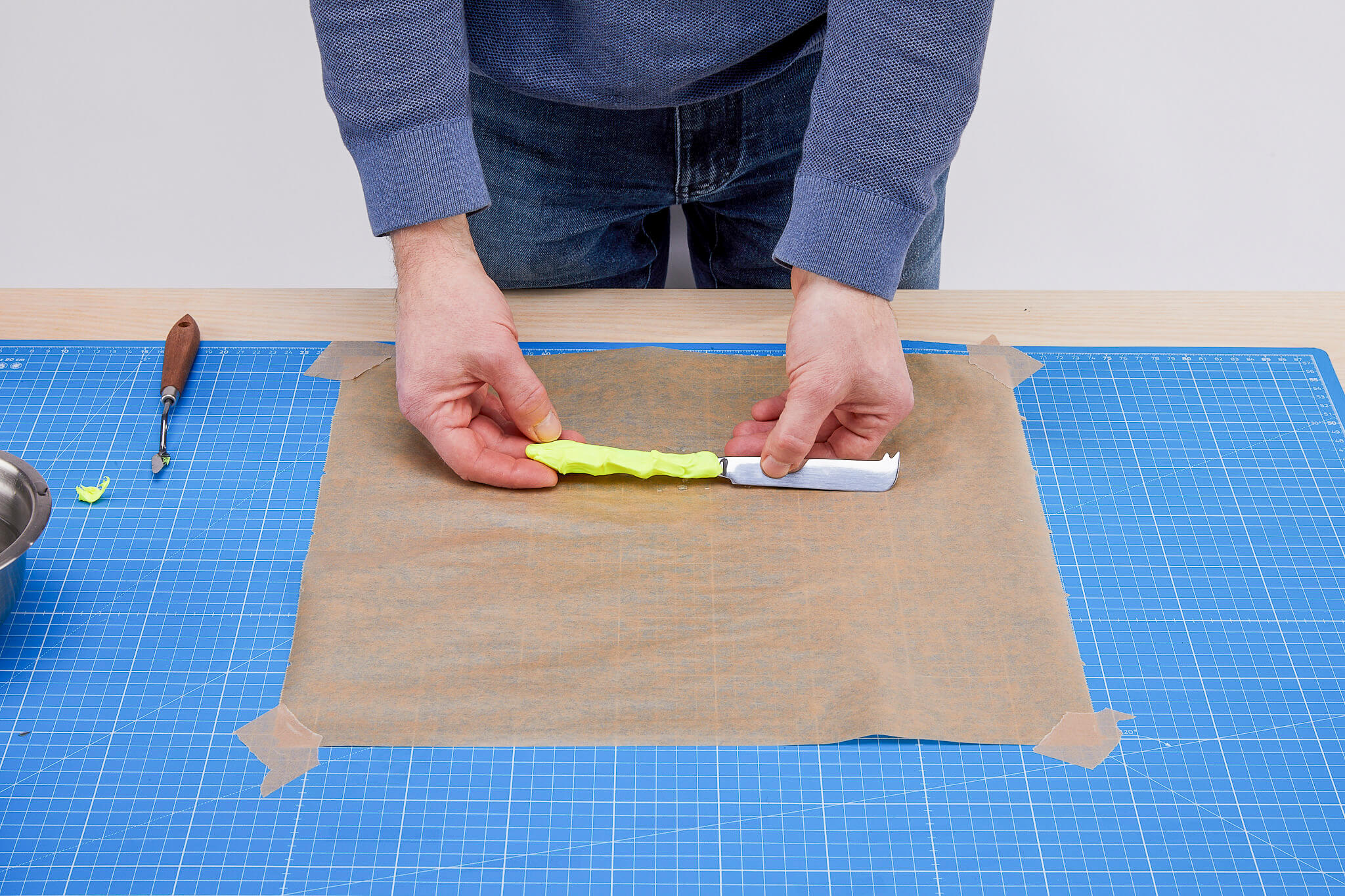
Varaform – kann auch kleben
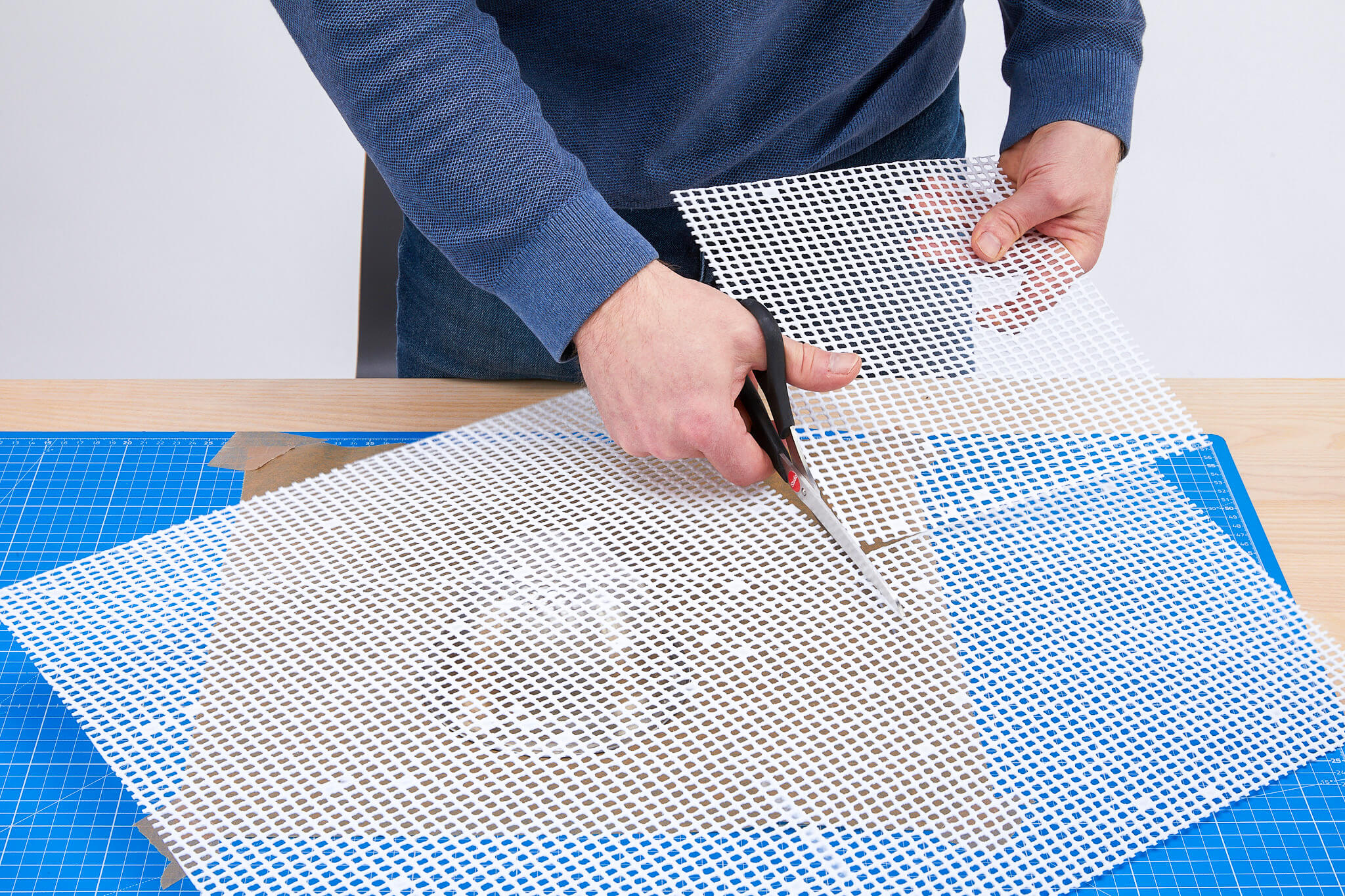
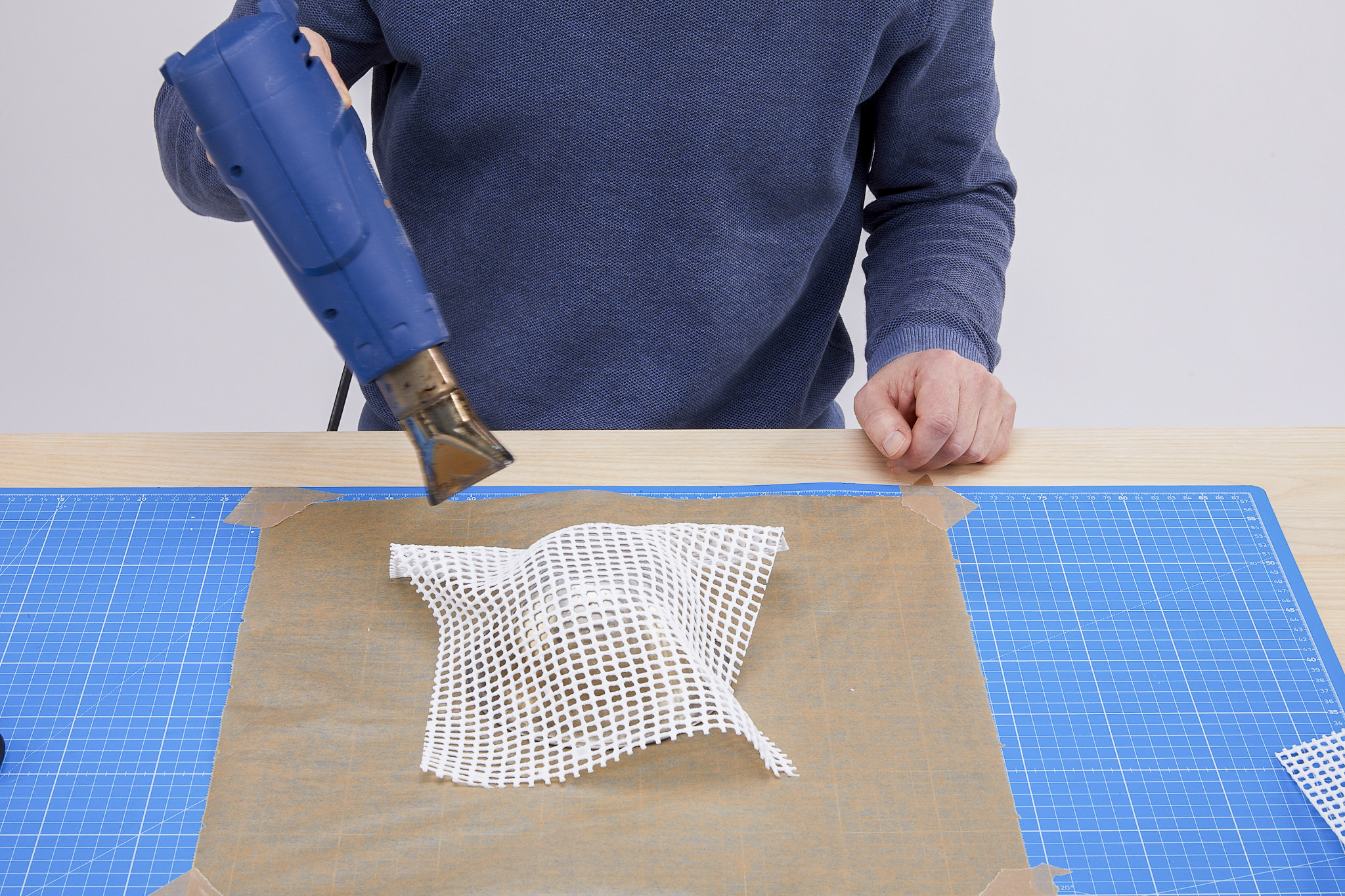

Während Worbla, Thibra und Formcard in Plattenform angeboten werden, kannst Du das aus der Medizintechnik stammende Varaform als Rollenmaterial bekommen. Varaform besteht aus einem Baumwollgewebe, das von einem Kunstharz umschlossen ist. Diesem thermoplastischen Kunstharz wird die biologische Abbaubarkeit zugesprochen. Aus drei verschiedenen Maschenweiten kannst Du wählen und damit feiner oder gröber Formen abnehmen oder frei gestalten. Bei 70 °C ist das Material am besten formbar, ohne zu kleben. Erwärmst Du es darüber hinaus, wird es klebrig. Mit diesen Eigenschaften kannst Du gut arbeiten, denn Varaform lässt sich beispielsweise mit dem Heißluftfön bereichsweise in den klebrigen Bereich erwärmen, damit Du es dort mit anderen Teilen verbinden kannst. Verwende am besten beim Abformen dünne feuchte Tücher oder andere dünne Trennschichten zwischen Original und Varaform, damit nicht versehentlich das Material mit dem Original verklebt. Darüber hinaus empfehlen wir bei allen Arbeiten mit allen in diesem Artikel genannten Materialien eine Unterlage aus Silikon auf dem Tisch zu verwenden. Sie ist temperaturunempfindlich und auf ihr haftet kein klebriger Thermoplast.
Thermoplaste entsorgen
Wie meist bei Kunststoffen steht einem wirklichen Recycling – also der Wiederverwertung auf demselben Niveau – die sortenreine Trennung entgegen. Das exakte Identifizieren und das Sortieren der gesammelten Kunststoffe (oder das separate Sammeln) wären dafür zwingend erforderlich. Bei hunderten von Kunststoffen, die im Umlauf sind, ist dies mit dem heutigen System nicht realisierbar. Daher bleibt als nächste Variante das Downcycling (zum Beispiel das Zusammenmischen verschiedener Kunststoffe, um minderwertige Werkstoffgranulate daraus herzustellen) oder das energetische Verwerten in der Zementproduktion oder in einer Müllverbrennungsanlage. Letztgenannte Variante stellt zurzeit (mit 64 % der Gesamtmenge der Kunststoffabfälle in Deutschland im Jahr 2021, Quelle: Umwelbundesamt) den vorherrschenden Umgang mit Kunststoffmüll dar.